設備の稼働率と保全状況をリアルタイムに可視化 紙ベースの業務を大幅に削減し現場作業員の生産性を改善
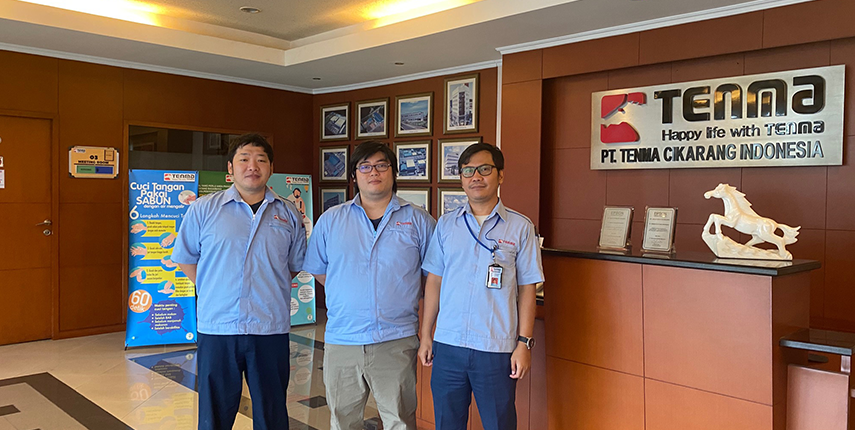
紙ベースでの記録から脱却し、集計データの精度が向上 現場作業員や事務員の業務負担を軽減
紙ベースの生産日報では正確さとスピードに課題
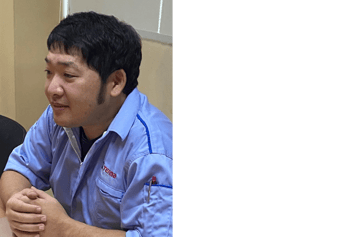
Vice President Director
小山田 祐美 氏
プラスチック総合成形メーカーの天馬株式会社では、生産拠点の1つであるインドネシアのチカラン工場の業務において3つの課題を抱えていた。1つ目は、正確な設備稼働率の把握だ。製造全般を統括するVice President Directorの小山田祐美氏は次のように振り返る。
「紙ベースの生産日報に頼っていたため、稼働率が正確性を欠いていました。稼働率を正確に把握できるかどうかは現場の配員計画の精度にも直結するため、改善が急務でした」
2つ目の課題は、稼働実績を把握するまでのタイムラグだ。生産日報が紙であるために手作業での集計が必要となり、工場全体の状況を把握できるようになるのは、翌日の午後であった。課題の3つ目は、最新の設備メンテナンス状況を一覧で管理できていないことだ。小山田氏は、「設備の状況を一覧にして可視化するだけでなく、メンテナンスの計画や実施も効率化したいと考えていました」と話す。
ダッシュボードの使い勝手や導入しやすさを高く評価
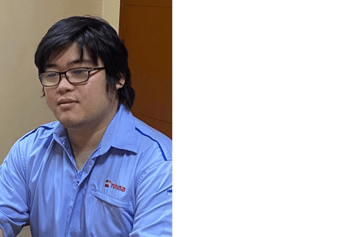
Manager
金城 奇龍 氏
こうした背景から、チカラン工場ではmcframe SIGNAL CHAIN(以下、SIGNAL CHAIN)の稼働モニタリング(OM)と設備メンテナンス(EM)を導入。SIGNAL CHAINを選定した理由について、小山田氏は次のように語る。
「数年前からmcframe生産・原価管理システムを導入していたこともあり、B-EN-Gインドネシアに相談しました。稼働モニタリングだけでなく設備メンテナンスもラインアップされていて同時に導入できることと、ソフトウェアが優れていることが決め手になりました。特にダッシュボードの使い勝手が良く、稼働実績や段取り時間といったデータを柔軟に取捨選択して抜き出せるのは便利だと感じました」
導入はまず稼働モニタリング(OM)から行われた。各設備の信号灯を有線LAN接続可能なパトライト社の積層情報表示灯「LA6-POE」に付け替え、そこからデータを抽出してSIGNAL CHAINに連携することとした。
チカラン工場のManager 金城奇龍氏は、「当初は無線接続の信号灯を採用する予定でしたが、電波調査の結果、設備が発するノイズのため断念し、有線接続としました」と語る。また小山田氏は「複数メーカーの機器があり、それぞれ配線が異なることから事前の調査には苦労しましたが、信号灯の設置やデータの取得に関してはスムーズでした。SIGNAL CHAINがシンプルで導入しやすい製品だったことも大きいでしょう」と振り返る。
導入はコロナ禍の最中に行われたが、同じく導入を担ったAssistant ManagerのAhmad Hidayatul Wildan氏は「B-EN-Gインドネシアからのサポートはすべてオンライでしたが、特に支障なくスムーズに導入を終えることができました」と話す。
データ収集の自動化で年間100万円相当のコスト削減
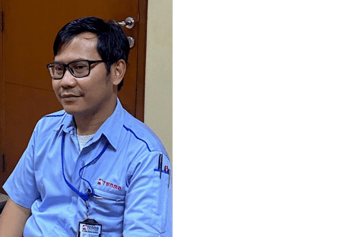
Assistant Manager
Ahmad Hidayatul Wildan 氏
SIGNAL CHAINの導入によって、チカラン工場では設備の稼働状況がリアルタイムに可視化され、レポート作成が柔軟かつ迅速になった。手書きの日報からデータ集計する業務が不要となったため、事務員2人相当の工数が削減できた。これは金額にして年間100万円程度のコストに相当する。
「現場の作業員は生産日報を一切記入する必要がなく、業務に集中できるようになりました。これまで以上の生産性向上が期待されます」(Ahmad Hidayatul Wildan氏)
またチカラン工場では以前より、トラブル発生時に責任者を呼び出すボタンを各製造設備に設置している。そのボタンからの信号をアンドンに表示させることで、呼び出しの回数や頻度もSIGNAL CHAINで見える化できるようにしたのだ。
さらに、設備の稼働実績をデータ化したことで、設備のコストを正しく製品に配賦できるようになり、原価計算の精度向上への先進的な取り組みにもつながっている。
スマートフォンからの入力でメンテナンス業務の効率を向上
また設備メンテナンス(EM)の導入によって、メンテナンス計画と実施状況をスマートフォン(Android)で容易に確認・入力できるようにしたことで、効率的なメンテナンスが可能となった。現場では項目を確認しながらメンテナンスを実施し、ボタンを押すだけで作業記録が完了するようになっている。また、スマートフォンで撮影した写真や動画をそのまま添付すると視覚的に確認でき、作業者が実際に保全したかどうかの証拠にもなる。
金城氏は「メンテナンス情報が正確になりました。また、履歴の入力が容易になったため、担当者は検査に集中できるようになりました」と話す。さらに小山田氏も「メンテナンス担当者が入力した結果をもとに、自動で『カルテ』を作成できるようになりました。以前は設備保全の実施状況を問われた際、履歴をたどるのが大変でしたが、今では常に最新の状況が示されるカルテなので直ぐに確認できます。また、緊急依頼や進捗の確認も一目瞭然です」と導入メリットを語る。
こうしたチカラン工場での成果を踏まえて小山田氏は、「今後はインドネシアのスルヤチプタ工場にも同様の仕組みを導入できればと考えています。また、SIGNAL CHAINの寿命管理とmcframe生産管理からの製造実績データを連携させ、設備ごとに金型の取り換え時期が分かるような予知保全の仕組みも検討しています」と話し、さらなる活用を見据えている。
設備のリアルタイムな稼働状況(左図 上)、点検スケジュール表(左図 下)とスマートフォンによる入力画面(右図)
導入企業概要
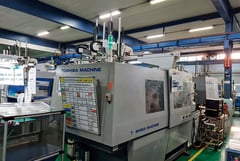
半世紀以上の歴史を有するプラスチック総合成形メーカー。長年に渡って培ってきた射出成形を中心とした成形・加工技術により、主に家庭用品、受託製造品、受注開発製品の3つの分野において高品質なプラスチック製品を顧客に提供している。
商号 | 天馬株式会社 PT. TENMA CIKARANG INDONESIA |
創立 | 1949年8月26日 |
---|---|
資本金 | 19,225百万円 |
従業員数 | 7,535名(連結)(2021年3月31日現在) |
事業内容 | プラスチック製品(家庭用品、自動車部品、OA機器部品、メディアケース、物流・農水産用資材、飲食用資材、建築資材など)の製造および販売 |
導入製品
mcframe SIGNAL CHAIN
※クリックすると製品サイトに移動します。
- 本事例は2021年8月現在の内容です。
- 本事例中に記載の肩書きや数値、固有名詞等は掲載当時のものであり、変更されている可能性があります。
- 本事例に記載されている社名、製品名などは、各社の登録商標または商標です。
- 掲載企業様への直接のご連絡はご容赦ください。